KBH Ceramic Connect
Innovative Solution for Cost-Effective Ceramic Integration
The KBH CERAMIC CONNECT system revolutionizes the use of ceramic slabs in landscaping and construction by offering a cost-effective solution to increasing material value. By bonding a thin ceramic slab to a robust, load-bearing concrete base, this system provides the aesthetic appeal of ceramics with the strength of concrete. The bonding process is seamlessly integrated on the wet side of production, making it ideal for both new installations and retrofits. With a modular design that allows for low initial investment, KBH CERAMIC CONNECT is set to transform the market.
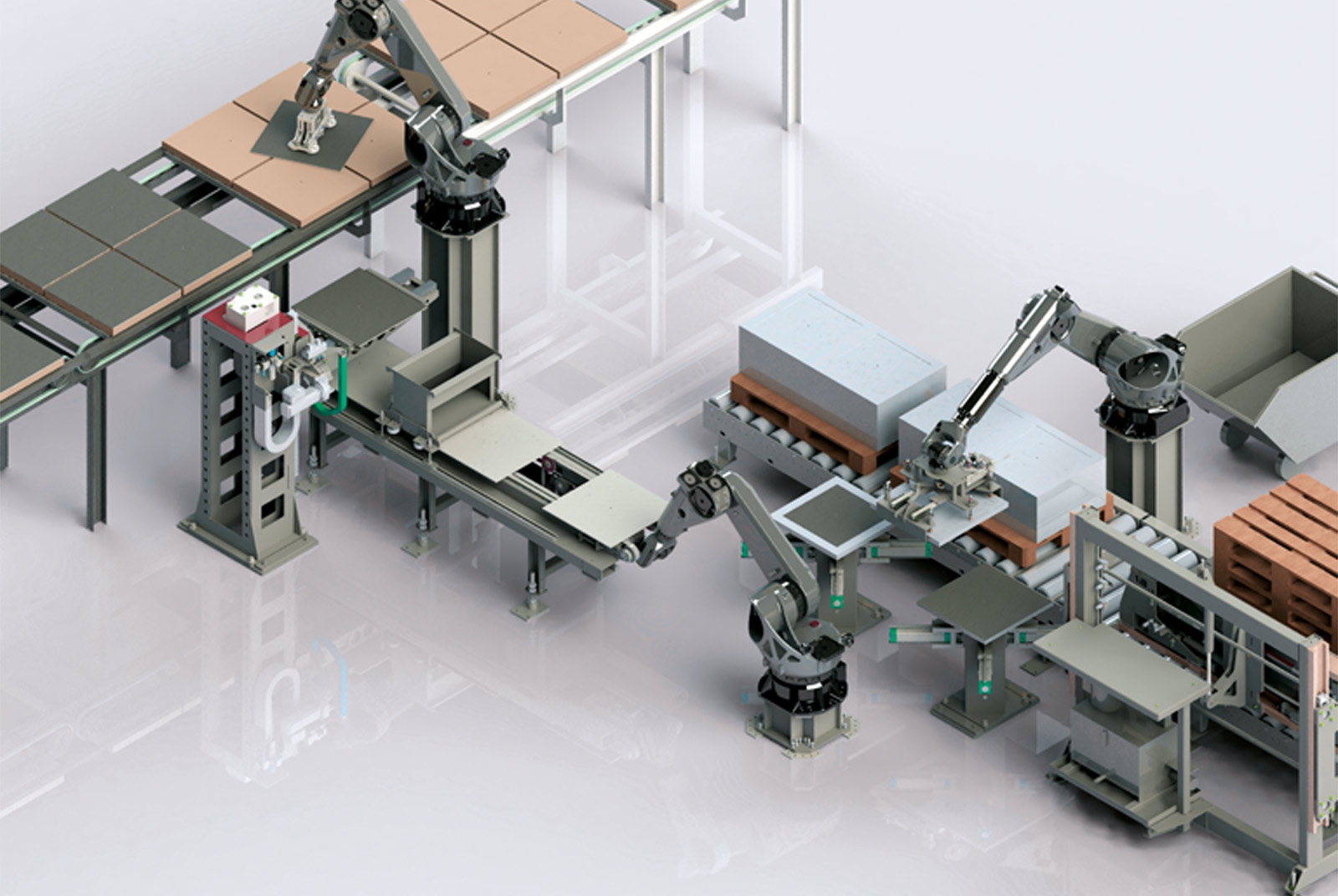
Quick Facts
- Innovation: Bonds thin ceramic slabs to durable concrete bases for cost efficiency
- Compatibility: Suitable for greenfield sites and retrofits in existing plant configurations
- Production: Utilizes standard paver machines to produce concrete base
- Bonding Process: Takes place on the wet side using a special adhesive developed in collaboration with KBH
- Handling Options: Available in semi-automatic and fully automatic versions
- Cost Efficiency: Provides a 30% - 40% cost saving compared to solid ceramic slabs
Working Principle
The KBH CERAMIC CONNECT system operates by transporting a ceramic slab face down through an adhesive application unit, where a special glue is applied. The slab is then rotated to present the adhesive side up for bonding with the concrete base. A robot picks up the prepared slab and places it onto the fresh concrete base. The innovative bonding technique developed by KBH activates the adhesive, ensuring a strong bond. The bonded product then moves into the curing chamber, where the bonding process completes without time constraints, allowing for a more effective adhesion.
Why Choose KBH CERAMIC CONNECT
- Cost-Effective: Significantly reduces costs by combining ceramics with concrete bases, saving 30% - 40% compared to full ceramic slabs.
- Versatile Installation: Ideal for both new plant installations and retrofits, making it a flexible solution for various production environments.
- Innovative Technology: Utilizes a specialized adhesive and bonding process developed by KBH to ensure strong and durable products.
- Automated Options: Offers both semi-automatic and fully automatic handling to suit different production needs and capacities.
Samples
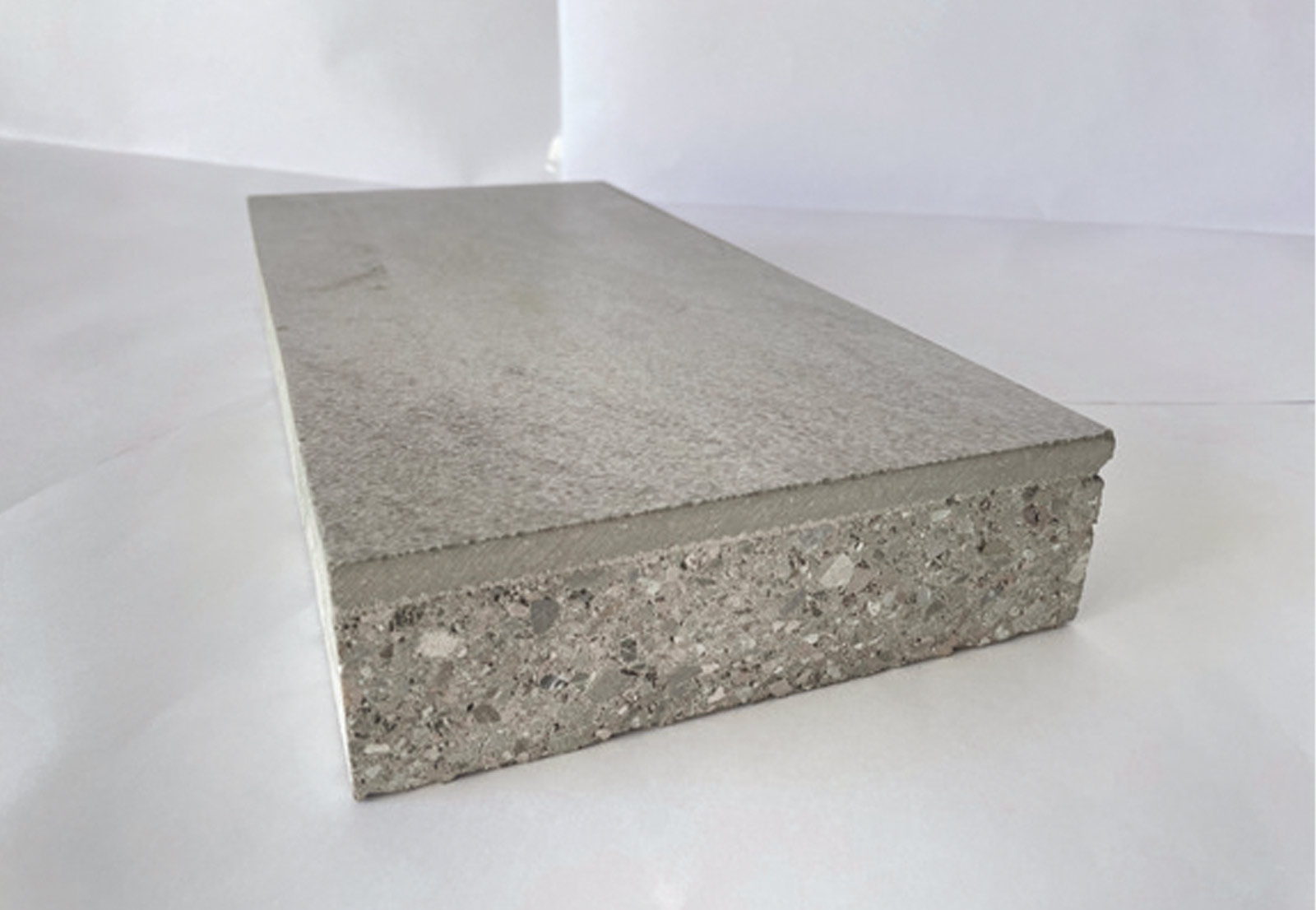
Downloads
Questions about the product
Do you have questions about our products?
Our product managers will be happy to answer all your questions at
+49 (0) 8331 - 9503-15